What Are the Most Weather-Resistant Plastics?
April 17, 2019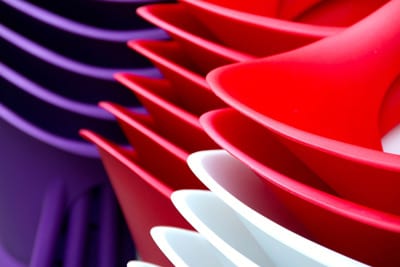
Low-Friction & Abrasion Resistant Plastics
June 20, 2019
Plasticizers are non-volatile chemical solvents used throughout the plastics industry to increase such properties as flexibility, pliability, durability, longevity, biodegradability, and extensibility in polymers. When added to a plastic or elastomer, plasticizers affect the properties of the material without fundamentally changing its basic chemical makeup. It also helps to improve a product’s elastic modulus upon completion. By modifying the type or amount of plasticizer, properties can be tailored to meet requirements like high tensile strength or even soften the material.
What Plasticizers Do
Plasticizers are found in many different materials and are among the most widely used substances in plastic. In fact, practically every type of plastic or polymer has one or more plasticizers added to it. Their discovery transformed the use and applications of the entire plastic industry. Plasticizers act like a lubricant among polymer chains to reduce rigidity. Without them, synthetic polymer materials would be too brittle and rigid for any practical purpose. For example, plasticizers give rubber its extensibility.
Approximately 90% of all plasticizers are used in polyvinyl chloride, or PVC. By volume, after Polyethylene (PE) and Polypropylene (PP), PVC is the third largest polymer used in products. PVC is one of the most durable materials in the world because of plasticizers added to it, lasting up to 50 years without damage. Because plasticizers can make the material stronger than before, PVC is largely used in the construction, automotive and wire and cable sectors. Familiar applications for PVC are pipes, sidings, window profiles, and medical devices. It is used for automotive trims and interiors, to make cables, PVC films, flooring, roofing and wall coverings, and much more. Plasticizers are also used in other polymers like acrylics, PET, polyolefins, and polyurethanes.
Types of Plasticizers
Plasticizers are constantly being evaluated for safety. Because of the widespread usage of plasticizers, they are widely researched and subjected to extensive testing for possible health and environmental effects. In the past sixty years, over 30,000 different plasticizers have been developed worldwide. Performance, availability, cost-effectiveness, along with health and environmental regulations, has limited a small portion, approximately 50, for commercial usage. Of these, varying types of esters are the more commonly used plasticizers. These are adipates, azelates, citrates, benzoates, orthophthalates, terephthalates, sebacates, and trimellitates produced by a reaction to isononanol or 2-propylheptanol alcohols and with such acids as phthalic anhydride or terephthalic acid. The combination of acids and alcohol create different properties for different applications.
Therefore, the plasticizer mixture affects the properties of polymers. Plasticizers can be used in combination or singularly to achieve the desired properties of the material. By changing the kinds of, amount, or concentration of plasticizer, the properties can be tailored to meet any application requirements of the material. For example, plasticizers can be used to control polymer degradation, and depending on the additive, can either increase or decrease the biodegradable rate. In effect, the plasticizer creates a disposable biodegradable biopolymer.
Plasticizers are valuable and essential to industries throughout the world today. Used as a common additive to polymer chains, it makes various materials more durable and more flexible, among other desired properties. Their widespread application has made plasticizers an indispensable part of the materials industry worldwide.
Contact the Experts at Osborne Industries
Osborne Industries specializes in thermoset plastic manufacturing, with the ability to create customized solutions for your application. With the use of plasticizers and other additives, Osborne’s completely customizable resin systems can be tailed to meet requirements for impact and abrasion resistance, corrosion resistance, flame resistance and smoke suppression, UV resistance, and more. To learn more about what plasticizers do and how our resin transfer molding and reaction injection molding can help improve your product, contact one of our experts today.