Plastic Design Guidelines for pDCPD
December 9, 2019A Guide to Fiber Reinforced Polymer Molding
March 5, 2020Comprehending the difference between thermoset vs thermoplastics, and which applications are suitable for each type, is often confused. Though thermoplastics and thermosets may seem similar, they actually have very different properties, and thus, industry applications. The differences between these two polymers are significant enough that understanding the behavior of each can ultimately help improve product designs and decisions.
Osborne Industries breaks down the differences between these two types of well-known polymers.
Thermosetting Plastics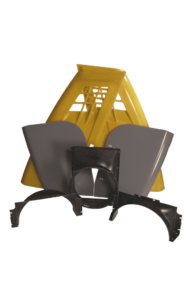
Thermosets, also referred to as thermosetting polymers or thermosetting plastics, are plastics that, after being cured, form an irreversible bond. Cured thermosets will not melt, even when submitted to extremely high temperatures, because the polymers in the material cross-link in an unbreakable bond during the process. These plastics are often processed by reaction injection molding (RIM) and resin transfer molding (RTM).
Due to the intense strength from cross-linking during the curing process, thermosets are ideal for applications requiring high heat deflection temperatures, such as under-hood parts of transportation and industrial equipment. Thermosets can also improve a product’s mechanical properties by improving heat and chemical resistance, as well as structural integrity. Thermoset plastics are often used for products requiring a seal due to their deformation resistance, and some thermoset families like polydicyclopentadiene (pDCPD) are considered among the most impact-resistant plastics available.
Thermosets play an important role in the plastic fabrication industry, serving unique purposes for each process. Plastics used for the resin transfer molding (RTM) process include polyester, vinyl ester, and polyimides. Plastics used for reaction injection molding (RIM) processes include pDCPD (polydicyclopentadiene), polyurethanes, polyureas, and structural foams.
Pros of Thermosets
- Flexible design
- Higher heat resistance
- Cost-effective
- Ability to mold variable wall thicknesses
- High dimensional stability
- Chemical-resistant
Cons of Thermosets
- Non-recyclable
- Challenging to surface finish
- Not able to be remolded or reshaped
Thermoplastics
Thermoplastics are any plastic material that can be melted and reshaped repeatedly, often found in the form of pellets. The higher the heat, the softer and more liquid these pellets become. This curing process is totally reversible since no chemical bonding takes place, which means that thermoplastics can be reused with minimal damage to the physical properties.
Because they’re malleable, they are used in a large variety of manufactured products. Thermoplastics can be found practically anywhere, from non-stick cookware and clothing to lab equipment and electronics. Some common examples of thermoset plastics include acrylic, nylon, teflon, polypropylene, and polystyrene.
Pros of Thermoplastics
- Recyclable
- Surface texture options
- Reusable with reshaping capabilities
- Chemical-resistant
Cons of Thermoplastics
- Will melt if heated to a certain temperature
- More expensive upfront costs compared to thermosets
Differences Between Thermosets vs. Thermoplastics
As you now know, the primary difference between thermoset vs thermoplastics is structural integrity. Thermoset polymers have a higher temperature resistance, both hot and cold – they strengthen when heated and do not warp in extremely cold temperatures, but cannot be remolded. Thermoplastics have a low melting point yet can be reused without causing any chemical changes.
Essentially, thermosets offer all the benefits of thermoplastics with additional strength, durability and corrosion resistance.
Reaction injection molding (RIM) with thermosetting polymers uses significantly less pressure and heat compared with thermoplastics, meaning RIM can be performed at a lower cost. Thermosets have an advantage in flowability as well – the liquified polymer easily fills each corner of a mold so that more complex geometric shapes can be produced in one mold, rather than creating separate smaller parts to be joined together later.
Contact the Experts at Osborne Industries
Osborne Industries is an innovative plastic molding company, whose specialty in custom thermosetting plastic molding has produced parts for leading companies across the nation for more than 45 years. To learn more about thermoset vs thermoplastics custom molding capabilities, contact us today.