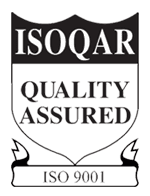
Osborne Industries, Inc., Announces Certification to ISO 9001:2015
June 18, 2018The History of Thermosets
July 18, 2018The applications and uses for thermosetting plastics have grown substantially over the years. The success and benefits of this type of plastic is due in large part to its favorable plastic properties. Thermoset plastics polymers cross-link together when curing to form an irreversible chemical bond. It is one of two organic polymer-based plastic materials, the other being thermoplastic. However, the difference between thermoplastic vs. thermoset plastics lies in their ability to be remelted or reshaped; thermoset plastics permanently form a rigid three-dimensional structural network that immobilizes the molecules.
Why Are Thermoset Plastics Used?
Thermoset plastics offer enhanced:
- Chemical resistance
- Heat resistance
- Structural integrity
Thermosetting composites are created on a continuing basis to keep pace with the growing amount of complicated industrial applications. Thermoset plastic composites meet the material specifications of a huge variety of other production materials, at a much lower cost. Thermoset injection molding allows for a wide assortment of large and small parts. Huge volume requirements can be reached easily, and high-quality products can be delivered consistently through continuous batch processes. More importantly, complex, detailed geometric shapes that cannot be produced with metals or thermoplastics can be wholly produced in the mold itself. In this regard, thermosets offer an attractive alternative to metals and thermoplastics due to its exceptional physical properties and surface appearance, with little to no shrinkage when removed from the mold.
Thermoset Plastic Applications
With a combination of thermal stability, performance, and chemical resistance, thermoset plastics are extensively used in a wide variety of industries—from the manufacturing of electrical components and durable manufactured goods to the aerospace industry, heavy duty construction equipment, the energy sector—including oil, gas, and solar—and automotive manufacturing. Common products and applications that are made from thermoset plastics include construction equipment panels, electrical housings and components, insulators, cell tower tops, heat shields, circuit breakers, agricultural feeding troughs, motor components, and disc brake pistons. In short, thermosets and their composites can be found in all markets and sectors.
Utilizing the thermoset plastic manufacturing process, some great benefits of thermosetting materials are their light weight and flexibility. Thermoset composites remain stable in all environments and at many temperatures, too. Parts are dimensionally stable and structurally sound, and can be processed at low pressures and viscosities with reinforcing composites such as fiberglass, carbon fiber, or Kevlar to produce an incredibly strong, durable material.
Thermosetting Plastic with Osborne Industries
Osborne Industries, Inc., is a leader in the field of liquid molding of thermoset plastics via Resin Transfer Molding (RTM) and Reaction Injection Molding (RIM). Osborne’s 45 years of practical experience includes the manufacturing of paneling for heavy and lightweight construction equipment, cell cover tops for chlorine generation, aerial lift buckets, agricultural equipment and much more.
Osborne chemists work with a range of thermoset materials from rigid fiberglass-reinforced plastics, elastomeric polyurethanes, to impact and corrosion-resistance pDCPD (polydicyclopentadiene) to produce cutting-edge products for our clients and customers. As a custom molder, Osborne Industries has the expertise to offer innovative solutions for your most demanding projects! To learn more about uses for thermosetting plastics, contact us today.