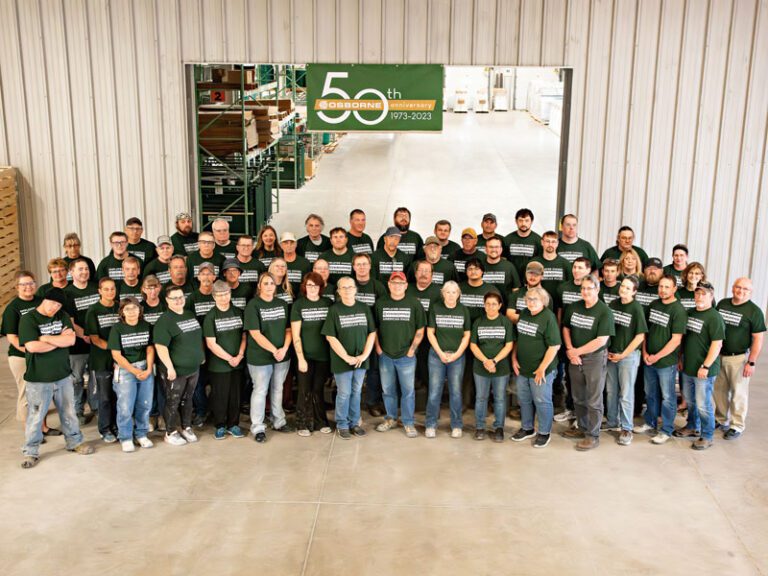
Osborne Celebrates 50 Years
May 23, 2023Three Common Reinforcing Materials for Plastics
August 16, 2024In 1976, Osborne Industries, Inc., originated the closed molding method that would later be known in the plastics industry as resin transfer molding, or RTM. The process of RTM involves mixing resin with a catalyst and then injecting that mixture into a closed mold with pre-loaded reinforcing material like fiberglass. It is often used to make components with complex shapes, smooth finishes and large surface areas.
Thanks to a low environmental impact and a wide range of reinforcement options, RTM services have long been a popular method of fabrication for composite parts, and a variety of industries have taken interest in its benefits. Aerospace and transportation manufacturers can use RTM molding for control panels and wheel covers, medical equipment producers might implement RTM for housings of machines, and those in agriculture have likely seen it used for tractor or heavy machinery parts.
One reason RTM is popular is because it can be customized depending on your needs and specifications as a manufacturer. For example, an under-hood component of a tractor may need to be abrasion resistant, while a frame for a window panel on the same tractor may require smoke-suppressant properties. Because RTM is a customizable, flexible process, it can easily accommodate the contrast of requirements in complex machines and products.
In RTM customization, everything from color and hardness to resistance against abrasion and heat is made-to-order. This customization is in part due to the variety of different fiber types available for RTM composites. Before the preform — or contoured reinforcement — can be created, the optimal type of fiber to use must be determined.
At Osborne, our most popular fiber-strengthening components are fiberglass and include mats and woven rovings. CompositesWorld defines fiberglass mats as fibers combined with a chemical binder and woven rovings as an inexpensive, thick material used when high reinforcement is needed.
Over the years, products molded using Osborne’s RTM services include:
- Aerial lift platforms/buckets
- Bus and vehicle window panels
- Industrial blower housings
- Forklift body parts
- Hog feeder and agricultural products
- Industrial cab parts
- Light armor military cases
- Machinery covers
- Medical bed tubs
- Medical chair specialty seating
- Medical instrument covers
- Truck and tractor fan shrouds
- Water sampler housing components
- Water treatment parts
With decades of experience in RTM manufacturing, Osborne can provide turnkey guidance for your next plastic project from concept to prototype to final product, and from patterns and molds to final inspection. To learn more about our RTM services or plastic molding capabilities, please contact us today.