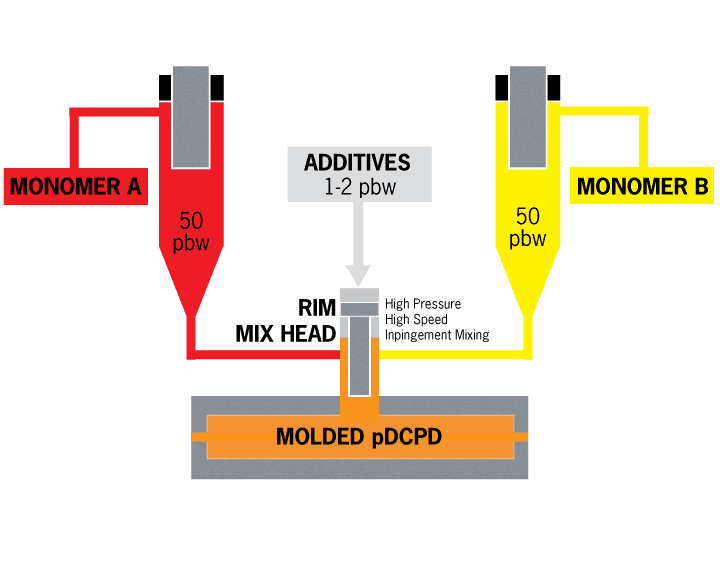
What is pDCPD? Your Questions Answered
August 31, 2016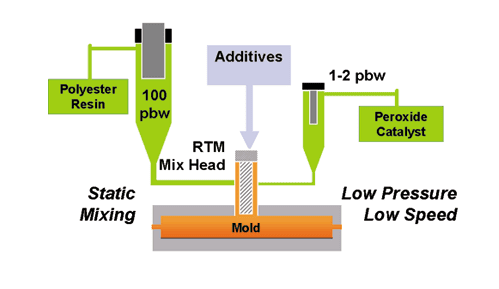
How the Resin Transfer Molding Process Works
March 16, 2017Benefits of pDCPD Reaction Injection Molding
When we had a customer that was looking for alternatives to the sheet metal hoods on boring machines used in the construction industry, Osborne offered pDCPD reaction injection molding (RIM) as a solution to the problems they were facing. The wet conditions on many construction boring jobs led to excessive rust on the steel hoods, while the rugged environment dented and damaged the sheet metal. As opposed to steel, pDCPD offers an excellent combination of chemical and corrosion resistance, as well as outstanding impact resistance. These characteristics made the engineered thermoset polymer the perfect replacement for the sheet metal hoods.
The Structural and Ergonomic Advantages of Using RIM pDCPD
Also known as Polydicyclopentadiene, pDCPD provides other advantages, including improved worker safety, due to:
- Lighter, easier-to-lift parts compared to their sheet metal counterparts.
- Fewer handling injuries because pDCPD allows for ergonomically and user-friendly molded part edges instead of sharp edges created by thin sheet metal.
The part conversion provided additional advantages for our customer because we manufactured the hoods using reaction injection molding, a thermoset molding process offering inherent benefits that enable part consolidation. These benefits include:
- Polymer chains that act as strengthening backbones in the molded product.
- Mold-in inserts.
- Decreased energy usage and tooling.
For instance, using RIM to manufacture the hoods allowed us to incorporate brackets and a part stiffener into the design, creating a one-piece (rather than the original eight-piece) hood. RIM also eliminated the need for the costly fabrication and assembly required for the sheet metal hood. This, in turn, allowed for lower labor costs and faster post-tooling production times for the pDCPD hood.
Custom Reaction Injection Molding for Any Industry
In the end, this metal-to-plastic conversion not only met our customer’s stated need for a more durable hood, but also exceeded the company’s expectations by creating a unified part that provided better worker safety and faster production times. Molded pDCPD via Reaction Injection Molding may be the answer to your next project’s requirements. Contact Osborne Industries to speak with an expert today!