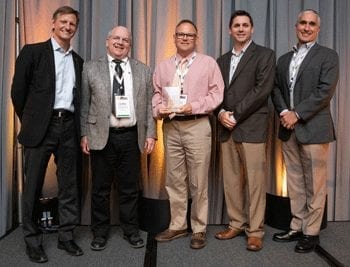
Osborne Industries, Inc., Named a Top Supplier for Altec
June 28, 2019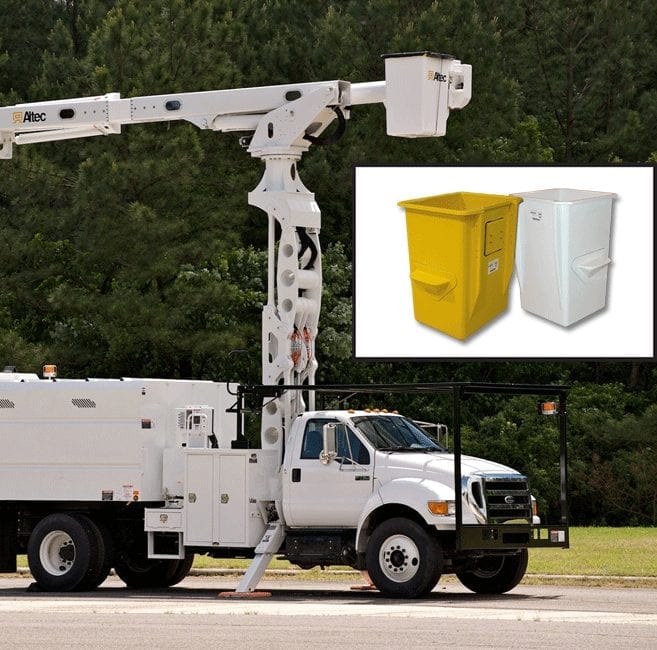
RTM and RIM Material Selection for Industry Applications
October 8, 2019Custom injection molding and die-cast molding have been compared for decades. When it comes down to a side-by-side comparison, companies that convert from metal to plastic experience many benefits from the transition. Plastic components are superior to metal in more ways than one, including strength and impact resistance, weight, and design flexibility. We break down each major component to keep in mind when considering a metal to plastic conversion.
Benefits of Metal to Plastic Conversion
There are various advantages of using plastics as opposed to metal. Some of the primary examples include:
- Lower manufacturing costs
- Better design flexibility
- Reduced part size
- Durability
- Consistent manufacturing
- Less maintenance
Cost-Effectiveness
First and foremost, the cost-effectiveness of plastic molding, like Resin Transfer Molding (RTM) and Reaction Injection Molding (RIM), versus die-cast molding is substantial. There is a large cost reduction with plastic simply because the material is cheaper. Saving on your production allows you to save your customers money in the long run. With processes like RTM, composite tools can sometimes be utilized. The investment in composite tools is substantially less than metal tooling.
In addition to upfront material and tooling savings, there are several long-term savings that come from using plastic, including material market stability, energy savings, and lower operating and shipping costs due to weight and flexibility.
Better Design
There is a lot of freedom that comes with custom plastic injection molding. Especially when it comes to aesthetics, “custom” is the key word. Plastics are versatile, with availability in essentially every color and a variety of surface finishes and textures to choose from. They have the ability to integrate complex geometries and shapes while also consolidating parts, so it is easy for engineers to creatively mold plastics for whatever applications they are working with.
Reduced Part Size
Depending on the application, size can be a major component when manufacturing for specific industries. When there are tight space restrictions, plastic is the answer! For any small appliances such as medical equipment or technology devices, injection molded parts are thinner, lighter, and overall smaller than their metal counterparts. For large parts, like those used in large industrial machinery, agricultural equipment, or transportation, converting from metal to plastic can significantly reduce weight – sometimes in the hundreds of pounds in the overall, finished equipment weight.
Increased Durability
The plastics used in manufacturing have come a long way – so much so that they can withstand a huge amount of stress and tolerance, which makes them just as reliable, if not more so, than metal parts. Many plastics, like polydicyclopentadiene (pDCPD) manufactured via RIM, are corrosion resistant, extremely impact resistant, and heat resistant, so it’s easy to design plastic parts to meet specific application or performance requirements. It’s been found that, on average, the tooling life for plastic parts is anywhere from six to ten times longer than for cast metal.
Impact resistance is extremely important for parts or equipment exposed to extreme conditions, like those found in agricultural equipment, wastewater treatment facilities, or chemical-processing plants. The impact resistance of metals cannot compare to many plastics, including the extremely impact-resistant pDCPD. These highly engineered plastics can keep the equipment they are used on running longer and reduce the need for repairs.
Consistent Manufacturing
When you consider plastic injection molding from a manufacturing standpoint, there is significantly more consistency in the process and outcome than with its metal counterparts. Manufactured products end up being more consistently uniform.
Plastic injection molding also provides the capability to combine various components into one single mold design, rather than creating several pieces and having to assemble them. This saves time, energy, and money, ultimately leading to decreased costs and faster production for the customer.
Less Maintenance
Plastic components are very low maintenance – unlike metal, they don’t need surface finishing or coating to protect the material. Changes can be made easily without needing a complete redesign, and the process typically requires minimal supervision, ultimately reducing labor.
Contact the Custom Injection Molding Experts
Ultimately, the best resource for education about custom plastic injection molding over die-cast molding is the molding companies themselves! To learn more about metal to plastic conversion, and the benefits of custom injection molding, please contact the experts at Osborne Industries today!