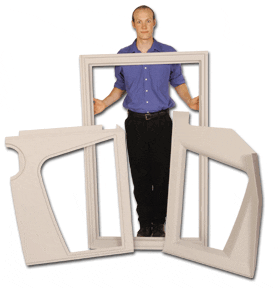
Top 4 High Temperature Plastics
February 11, 2019Osborne Joins Farm Equipment Manufacturers Association
March 21, 2019The manufacturing of plastic parts and products is an integral part of the global economy. A variety of plastic fabrication methods are performed to manufacture components for every industrial sector—medical and pharmaceutical, aerospace, shipping and packaging, electronics and electrical, automotive, transportation, durable goods and household items, construction, heavy equipment, agriculture, and so much more.
There are many types of plastic molding and methods used in manufacturing. Which plastic fabrication method is used depends on such factors as the product or part itself, its application, its size and shape, whether it requires thermoset or thermoplastic material, or high or low volume production rates. The following five plastic fabrication methods offer examples of the different kinds of plastic molding used for different manufacturing processes.
Hand Layup Molding
The oldest open molding process, the hand layup fabrication method, is often referred to as the most basic of the thermoset composite methods. The method is labor-intensive and suited for low volume production of large components like showers, boat hulls, tubs, and storage tanks. It consists of placing plies, which are reinforcing layers of woven fabric, mats, or even glass, manually into an open mold. The fabric may be pre-impregnated with resin or resin may be poured, brushed, or sprayed over and into the plies. Lamination of the structure is achieved by pressing out the trapped air by rollers or squeegees. Resins that cure at room temperatures, such as those for polyesters and epoxies are the most commonly used in the hand layup method. Curing is initiated by a catalyst in the resin matrix without heat, hardening the fiber-reinforced resin composite.
Hand Layup Molding Advantages
- Low tooling cost
- Excellent for large parts
- Wide selection of material types
Hand Layup Molding Disadvantages
- Not good for small parts or high volume runs
Injection Molding
Injection molding is a versatile, automated process used to fabricate detailed three-dimensional components. It is often utilized to form thermoplastic materials into components at high production rates and with very good dimensional accuracy. Resin pellets, the plastic material, are injected under high pressure into a relatively cool mold to allow the plastic material to solidify. The mold cavity determines the external shape of the component or product. Once cooled, the mold opens and the finished part or product is ejected. Because it is a discontinuous process where the component or item is formed, cooled or cured in the mold before ejection, it is a favored method for high volume production. Injection molding is used to produce a wide range of items, products and parts from lawn chairs and containers to toys and automotive parts.
Injection Molding Advantages
- High dimensional accuracy
- Good for high volume production
Injection Molding Disadvantages
- High initial tooling costs
- Low volume runs are expensive
Blow Molding
Blow molding is an automated fabrication method best suited for producing hollow components with uniform wall thickness, such as plastic bottles. The method inflates a heated plastic tube until it fills a mold and forms the desired seamless plastic part or product. There are a number of variations in the blow molding process—extrusion, injection or stretch molding—that require a preform called a parison, compressed air and a mold to shape the final container. The process of blow molding begins with resin pellets melted at high temperature. They are then preformed into a starter shape by injecting the hot material at high pressure into a specialized mold called a parison. Once the parison is filled to the required capacity, it is separated off and cooled. This preform starter shape is then reheated until soften and positioned in a stretch-blow-molder. A push rod fits the preform into the mold and a burst of high pressure air is blown (between 50 and 100psi), stretching and expanding the preform into the desired shape. The plastic is quickly cooled and the plastic shape is hardened.
Blow Molding Advantages
- Good for any hollow part with uniform wall thickness
Blow Molding Disadvantages
- Cannot be used to produce non-hollow parts
Resin Transfer Molding (RTM)
Resin Transfer Molding (RTM) is a closed-molding process where a liquid resin is mixed with a catalyst and injected into a closed mold that contains a type of dry fiber, typically fiberglass. A mixhead regulates the ratio of liquid resin (a common one being polyester) to catalyst. The mixture of resin and catalyst is injected at low pressure into the mold at a relatively low temperature. The resin mixture saturates the fiberglass creating a strong bond. Reaction time for the resin is measured in minutes. The RTM method is used to manufacture parts that need a structurally sound and smooth, finished surface on both sides of the part. Parts like electrical enclosures, machine or instrument covers or body parts, medical equipment, wastewater treatment tanks and forms, and many more are good candidates for RTM.
Resin Transfer Molding (RTM) Advantages
- Can utilize low-cost composite tooling
- Excellent for large parts with ribs, bosses, or other features on both sides of the part
- Lightweight and durable
Resin Transfer Molding (RTM) Disadvantages
- Not good for extremely small parts or high volume runs
Reaction Injection Molding (RIM)
Like RTM, the RIM, or Reaction Injection Molding process, begins with two (2) liquid resins. Rather than a liquid resin and catalyst, RIM uses an isocyanate component and a polyol resin mixture (sometimes polyurethane or pDCPD). The liquids are fed to a mixhead through supply lines at high pressure. Valves open in the mixhead and the liquids enter at high speeds and are mixed by high-velocity impingement. The mixture is then injected into a closed mold where an exothermic chemical reaction takes place, forming an irreversible polymer. Reaction time for RIM is measured in seconds. Manufactured parts with RIM can include extremely large, corrosion-resistant parts for chemical processing or wastewater treatment, automotive fenders or equipment body parts, agricultural equipment and machinery like tractor or combine parts, and much more.
Reaction Injection Molding (RIM) Advantages
- Lightweight and flexible compared to metals
- Superior corrosion and impact resistance
- Parts with complex geometries are easily molded
Reaction Injection Molding (RIM) Disadvantages
- Higher raw material costs as compared to injection molding with thermoplastics
To learn more about plastic fabrication methods used at Osborne Industries, please contact us today!