7 Advantages of Working With a USA Injection Molding Company
January 18, 2022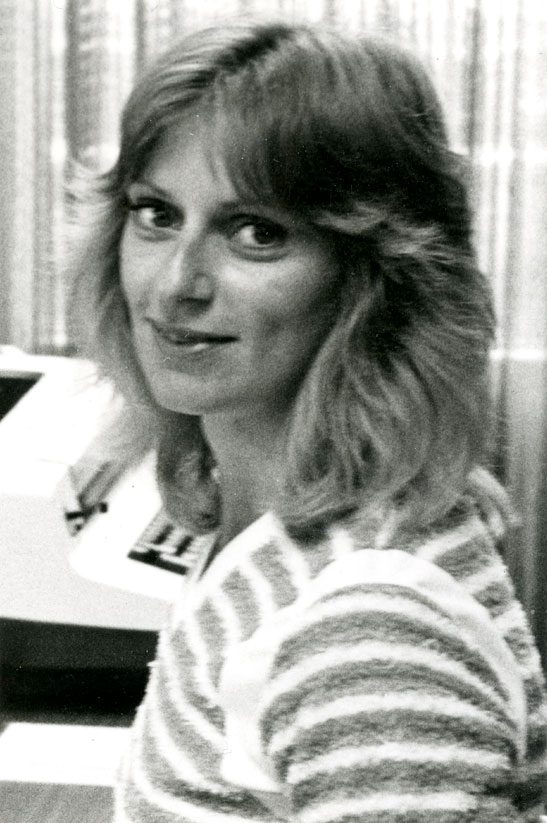
Corbett retires after decades-long career at Osborne Industries, Inc.
August 26, 2022Manufacturers in nearly every industry use prototypes to test new products and how they work in real-world situations. It’s a cost-effective way to iron out any issues with a product or part and is an essential step before beginning mass production. Plastic prototypes can be made using a variety of methods, including 3D printing and rapid injection molding. Prototyping plastic components on products isn’t really different from prototyping with other materials, requiring manufacturers to follow the same basic process.
Prototyping Plastics: Considerations When Designing Components
The complexities involved in designing new parts require that manufacturers overcome numerous hurdles, with many of these resolved by prototyping. Plastics are used for a wide variety of parts due to the material’s versatility, along with its multiple types that offer a diversity of properties.
Considerations for prototyping plastic normally include:
- Choosing the best materials for prototyping and for the finished part or product
- Creating the plastic prototype by utilizing the most suitable materials and molding machinery for the stock.
- Designing the piece in a way that it’s suitable for multiple reproductions.
- Examining how specific components within the finished product function mechanically due to the design.
- Looking at the design and how it affects the functioning of the completed product.
The first step in prototyping plastics entails creating a digital version of the part or product, using a computer-aided design (CAD) model. This representation shows the manufacturer how the piece should look upon completion.
Four Ways to Prototype Plastic Components
Though the reasoning behind developing a prototype may differ slightly, every industry uses prototyping. Plastic components are used widely, and the basic reasoning behind prototyping plastics is simple. Making one component as a tester to ensure it fits or works correctly within a product. It makes more sense than making a thousand components and finding they aren’t engineered properly. This is what prototyping seeks to prevent.
Prototyping plastics is primarily done in one of these four ways:
- 3D Printing: Used due to its reasonable price and adaptability. While 3D printing allows for testing fit, it does not allow for functionality testing due to the brittleness of the material used in its production.
- CNC Machining: Works well for larger pieces or when needing special finishing. CNC machining may be used to machine a prototype out of various materials, including wood, metal, or plastic.
- Injection Molding: Allows for multiple prototypes and shortens the time from prototyping to mass production. For prototypes, injection molding can utilize lower-cost composite tooling prior to investing in aluminum or steel tooling for mass production.
- Casting: Quick and cost-effective method with advantages similar to both 3D printing and injection molding, but typically utilizes metal.
The primary advantage of plastic prototyping involves bringing products to market more quickly by shortening the design process so that production begins sooner. By bringing a design into real world situations, problems can be identified before parts are mass-produced, thus helping to prevent costly design oversights. Plastic prototypes allow designers to troubleshoot design problems and improve products before mass production.
Prototyping Plastics: Benefits of Using & Applications for Thermosets and Thermoplastics
Prototyping using plastics, whether with thermosets or thermoplastics, has both advantages and disadvantages, but may lend itself to allowing for improved fit and functionality testing over 3D printing or casting.
- Prototyping with thermosetting or thermoplastics offers the following advantages:
- Best option for products with thin wall thicknesses or that require flexibility.
- Easy to use for creating functional prototypes, particularly via injection molding or reaction injection molding (RIM) processes.
- Allows for full functionality testing with high resistance to impact and stress, tolerance to chemicals, and increased product robustness compared to wood or metal.
- Their ease of molding makes them a good choice for products with complex shapes or design features.
- Works well for aesthetically pleasing finishes for prototypes.
- Allows for use of composite tooling for prototypes, especially with thermoset materials, and can produce dozens of prototypes before the useful life of the tooling is reached.
Injection Molding for Prototyping Plastics
Though mass-produced products sometimes use injection molding techniques, these processes also offer a quick, affordable means for prototyping plastic components and products.
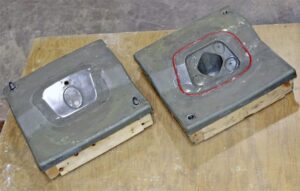
Low-cost composite tooling can be utilized to create prototype plastic parts via injection molding or reaction injection molding prior to investing in aluminum or steel tools for mass production.
Both typical injection molding with thermoplastics and reaction injection molding (RIM) with thermosetting materials may utilize a composite mold or metal die, into which either melted (thermoplastics) or liquid plastic resins (thermosets) are injected. The injected material experiences a chemical reaction, cools, and upon completion of the process, offers a plastic prototype with a superior surface finish and better mechanical properties than a part made via 3D printing.
Benefits of using injection molding for plastic prototyping include:
- Allows fabrication of a wide range of prototypes in various shapes, sizes, and weights.
- Ideal process for industries requiring extensive certification and testing, especially for medical applications.
- Offers a quick and cost-efficient method for testing conceptualities for products.
- Replicates a component reliably as per the finished product, allowing manufacturers to glean insights quickly into a prototype’s functionalities.
Overall, when it comes to plastic prototyping, injection molding with thermoplastics or thermosetting plastics saves both time and money. Osborne’s extensive experience in prototyping with thermosetting materials and thermosetting molding methods, like reaction injection molding (RIM), can help propel your project from concept to reality. For more information on prototyping with plastics, contact Osborne’s team of experienced professionals today.