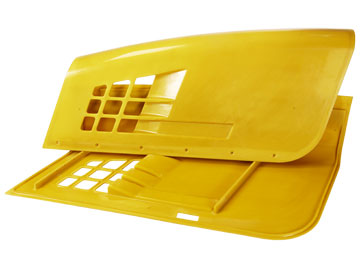
Top 3 Most Impact Resistant Plastics
August 21, 2017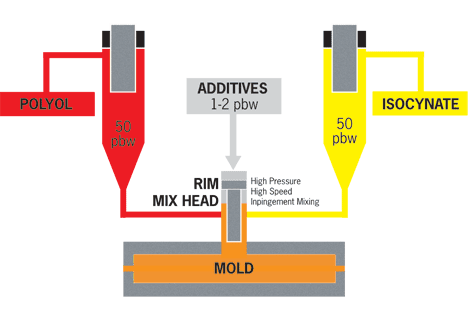
RIM Manufacturing Process: Step-by-Step
February 16, 2018The advantages of injection molding over die cast molding have been debated since the former process was first introduced in the 1930s. There are benefits, but also limitations to the method, and that, primarily, is need-based. Original equipment manufacturers (OEM) and other consumers who rely on molded parts to produce their goods, are looking for such factors as quality, durability and affordability in deciding which molded parts best suit their needs.
What is Injection Molding?
Injection molding is a method of creating finished parts or products by forcing molten plastic into a mold and letting it harden. The uses of these parts varies as widely as the variety of products made from the process. Depending on its use, injection molded parts can weigh from a few ounces up to hundreds or thousands of pounds. In other words, from computer parts, soda bottles and toys, to truck, tractor and auto parts.
Plastic Injection Molding vs Die Casting
The method of injection molding was originally modeled on die casting, a similar procedure in which molten metal is forced into a mold to produce parts for manufactured products. However, rather than using plastic resins to produce parts, die casting uses mostly non-ferrous metals such as zinc, aluminum, magnesium, and brass. Though just about any part can be cast from almost any metal, aluminum has evolved as one of the most popular. It has a low melting point, which makes it easily malleable to mold parts. Dies are stronger than the molds used in the permanent die process to withstand the high pressure injections, which can be 30,000 psi or more. The high pressure process produces a durable, fine grade structure with fatigue strength. Because of this, die casting use ranges from engines and engine parts to pots and pans.
Die Casting Benefits
Die casting is ideal if your company’s needs are for strong, durable, mass-produced metal parts like junction boxes, pistons, cylinder heads, and engine blocks, or propellers, gears, bushings, pumps, and valves.
- Strong
- Durable
- Easy to mass-produce
Die Casting Limitations
Yet, arguably, though die casting has its benefits, there are a number of limitations in the method to consider.
- Limited part sizes (maximum of about 24 inches and 75 lbs.)
- High initial tooling costs
- Metal prices can fluctuate significantly
- Scrap material adds to production costs
Injection Molding Benefits
The benefits of injection molding have gained in popularity over the years because of the advantages it offers over traditional die casting manufacturing methods. Namely, the immense amount and variety of low cost, affordable products that are made from plastics today are virtually limitless. There are also minimal finishing requirements.
- Light-weight
- Impact resistant
- Corrosion resistant
- Heat resistant
- Low cost
- Minimal finishing requirements
Suffice it to say, the choice of which molding method to use will ultimately be determined by the intersection of quality, necessity, and profitability. There are benefits and limitations in each method. Which method to utilize—RIM molding, traditional injection molding or die casting for part production—will be determined by the needs of your OEM.
Osborne Industries, Inc., utilizes the process of reaction injection molding (RIM) over traditional injection molding practices because of its even lower costs, durability, and production flexibility the method offers to OEMs. RIM-molding is suited in the usage of thermoset plastics as opposed to thermoplastics used in traditional injection molding. Thermoset plastics are light weight, exceptionally strong and corrosion resistant, and especially ideal for parts used in extreme temperatures, high-heat, or highly corrosive applications. Costs of RIM part production is low, too, even with intermediate and low volume runs. One of the major advantages to reaction injection molding is that it allows for the production of large parts, like vehicle instrument panels, chlorine cell tower tops, or truck and trailer fenders.