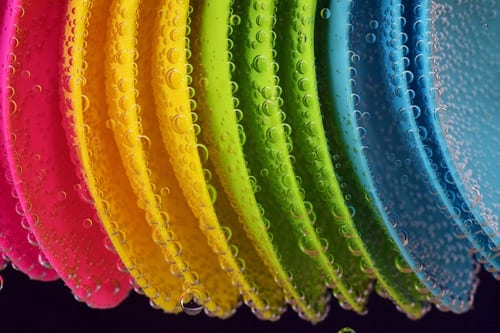
The Benefits and Limitations of Injection Molding
November 20, 2017The Properties of Plastic
March 19, 2018RIM, or reaction injection molding, was developed in the late 1960’s. Over time, technology has evolved along with the RIM manufacturing process itself, allowing Osborne Industries to tap into the numerous and unique benefits and capabilities of RIM for a wide variety of products. RIM produces thermosetting plastic resin parts by forcing low-viscosity liquid polymers into a design mold. The liquid material conforms to the mold’s shape, and after a chemical reaction, generates the end part. RIM is a very economical process for low-production volumes and large parts. It also provides manufacturers and designers with more creative opportunities and projects, as it can easily mold thin and thick walls in the same part. Below we examine the multi-stage RIM manufacturing process.
Steps of the RIM Manufacturing Process
1. Conditioning
To begin the RIM process, two or more types of liquid resins (typically polyol and isocyanate) are poured into separate holding tanks. The holding tanks are equipped with temperature and feed-control mechanisms. It is here where the plastics are conditioned to the correct temperatures, pressures, and gravities. Once properly conditioned, the plastics are ready to be injected into the mold.
2. Injection
Before the two liquids are injected into the mold, a dispensing unit switches to a higher pumping pressure. The liquid plastics are injected with a special valve called a mix head, which allows the complete mixing of the two liquids and produces a chemical reaction as the mold is filled with liquid material, for example, polyurethane or pDCPD (polydicyclopentadiene). The mold is filled quickly, depending on the type of resins used.
3. Cooling/Shrinking
After the mold is filled, the freshly molded part is allowed to cure in the mold for a short time. During the molding process, the part will shrink a slight amount. This is completely normal. Besides a few minutes of cooling, there is no other post-curing necessary for the part. It is immediately ready for use, or post-processing if needed.
Reaction Injection Molding Benefits
The RIM process is used across a broad spectrum of industries, such as automotive for bumpers, electrical for housing panels, and technology for computer and telecommunication equipment. Reaction injection molding provides an array of benefits, including:
- Extreme temperature resistance
- Suitable for a wide range of thermoset materials
- More cost-effective for larger parts than injection molding
- Varying wall thickness
- Lower cost tooling compared to injection molding
- Lower labor requirements than resin transfer molding
- Low energy usage
Interested in learning more about thermosetting plastic and thermoset plastic? Feel free to contact the experts at Osborne Industries or select a topic below!