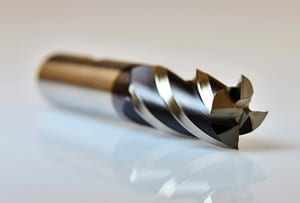
Comparing Thermoset and Thermoplastic Pricing
January 29, 20195 Popular Plastic Fabrication Methods
March 6, 2019Extreme heat resistance is one of the defining properties of high temperature plastic known as thermosets. Long touted for their light-weight and chemical-resistant properties, it is the high heat-resistance that makes the performance of thermoset plastics exceptional in demanding applications and environments.
Why Thermosets are the Best Temperature-Resistant Plastics
Several decades ago, the thermoplastics in use held promise as an inexpensive alternative, if not substitute, for metal, wood, or glass. Effective as the thermoplastics were, environmental factors like heat caused thermal degradation and wear. Though much lighter, the older-generation polymers could not provide the heat resistance that ceramics and metals could. Under high temperature conditions their performance was, overall, ineffective. The advance of thermoset plastics in the 1990s overcame these restraints, providing a higher degree of reliability, durability, and performance than the older polymers could.
The whole family of heat-resistant thermoset plastics can operate effectively at temperatures exceeding 120° C and up to 300° C. This high heat resistance is due to the process in which they are created. Monomers are heated to high temperatures and then mixed with a catalyst causing their molecular chains to cross-link. Catalysts not only help bond the monomers together to form a polymer, but enhance the material properties. There are a number of unique thermoset applications and uses, such as impact resistance, chemical resistance, friction and wear performance, dimensional stability, creep resistance, and most desirably, a heat-resistant, high-temperature plastic.
Here are 3 top heat-resistant plastics to consider for high-temperature applications:
1. Vespel®
Vespel® is well-known for its heat resistance. It is a non-melting polyimide that can withstand heating up to 300° C repeatedly without affecting its thermal or mechanical properties. Its popularity in large part is due to versatility in hostile and extreme environmental conditions. Unlike most plastics, Vespel does not produce significant out-gassing at high temperatures, which makes it ideal for lightweight heat shields and crucible support. Types of additive mixtures like graphite or PTFE give Vespel up to 350 hours of 398° C heat with losing only 50% of its initial tensile strength.
Vespel Applications
- Jet engines
- Industrial machinery
- Cars , trucks, buses, and other like vehicles
2. Torlon®
Torlon®, is another thermoset polyamide with exceptional long-term strength and stiffness up to a continuous 260° C. Torlon is considered an effective alternative to metal where high temperature friction and wear applications are present. It’s also known for its resistance to wear, creep, and chemicals, including strong acids and most organic chemicals. The thermoset is also an ideal material for use in severe service environments.
Torlon Applications
- Aircraft hardware and fasteners
- Mechanical and structural components
- Transmission and power train components
- Coatings, composites, and additives
3. Custom-Formulated Resins
For many years, plastic chemists have continually worked to develop custom composites that meet a variety of physical and mechanical property needs. For example, Osborne’s own chemists and research scientists have developed custom materials to meet the high-temperature and performance requirements of military fan shrouds. These composites must endure extreme temperatures experienced in the engine bay of FMTVs. These composite materials are proven to withstand heat deflection temperatures (HDTs) in excess of 300° C.
Custom Resin Applications
- Under-hood military vehicle fan shrouds
- Transmission and power train components
- Outdoor instrument housings
- Agricultural equipment body parts
4. pDCPD
When impact resistance is a must, design engineers can rely on Polydicyclopentadiene, or pDCPD, for short, for its extreme impact resistance and thermal stability. pDCPD is an extensively cross-linked polymer with heat-resistance and high heat deflection temperature of up to 120° C. The engineered thermoset polymer possesses exceptional mechanical and physical properties with chemical and corrosion resistance, stiffness, high tensile strength, impact resistance, and heat resistance. The molding flexibility of pDCPD has characteristics that are similar to expensive engineered thermoplastics and offers design freedom with virtually no limitation on part size or weight.
pDCPD Applications
- Large truck and bus body panels
- Agricultural and heavy construction equipment parts
- Corrosion-resistant chemical processing equipment
- Instrumentation housing
- Wastewater treatment equipment
Want to learn more about high temperature plastic for your applications? Click below to speak with our experienced team at Osborne Industries!