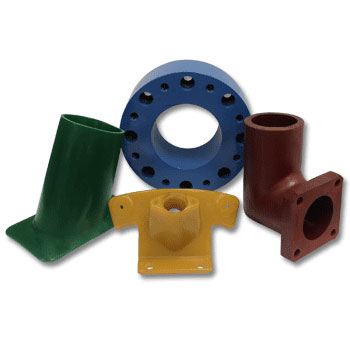
High Performance Composites Now Available in Custom Colors
September 14, 20217 Advantages of Working With a USA Injection Molding Company
January 18, 2022While used to make paints, adhesives and inks, dicyclopentadiene (DCPD) resin also offers a means to fabricate a variety of larger components through the use of reaction injection molding (RIM) techniques. A thermoset plastic used as a substitute for metals and concrete, DCPD is used in the fabrication of boat hulls, decks, farm machinery, fan shrouds, panels on vehicle bodies, protective shielding and other products that need to withstand high impacts and fatigue.
Producing Parts from Dicyclopentadiene Resin
Dicyclopentadiene resin results primarily from heating naphtha, crude oil, or other gas-based oils. Manufacturers use the RIM process to produce large parts with dicyclopentadiene resin efficiently and quickly. This method for molding allows the production of pieces that are several times that which other types of compression or conventional injection molding can produce. These products still retain the toughness, strength, and aesthetics for which DCPD is known. In fact, a prime benefit of using a RIM process to create parts out of dicyclopentadiene resin is the ease with which these larger components are fabricated.
Advantages & Properties of DCPD
DCPD offers quite a few advantages over materials like fiberglass, steel, wood, or other thermosetting plastics. It functions well even after repeated impacts, along with exposure to chemicals and heat. Due to its lightweight, vehicles with components like bumpers, fenders, and body panels made from DCPD are also more fuel-efficient.
Characteristics of DCPD include:
- Heat resistance
- Impact resistance
- Low viscosity
- Resistance to corrosive chemicals
During the RIM process, components with surface areas of up to 120 square feet (11.15 square meters) can be produced with DCPD. This surpasses the size of parts that can be made from other resins via RIM methods. As components made with DCPD do not require identical geometry for multi-cavity molds, engineers can also create more complex parts to enable more cost-effective solutions.
Parts made from DCPD have the following advantages:
- Allow for more variability in wall thickness
- Better aesthetics in surface finishes
- Can be made with larger surface areas
- Does not dent or rust
- Easily repairable
- Flexible yet durable
- Good strength to weight ratio
- Low average density
- Permit fabrication of parts up to 12 inches (about 30.5 cm) thick
Along with creating complex designs, the DCPD RIM process makes the fabrication of components far less expensive than those made from steel or other metals.
Using Reaction Injection Molding for DCPD Fabrication
Making large parts requires a closed mold and an environment with little moisture or oxygen. Using a catalyst like molybdenum or tungsten, two streams of dicyclopentadiene resin are injected at the same time, causing a chemical reaction. When the liquid DCPD and catalyst mix, heat quickly transforms the material within the mold into a solid thermoset. Parts normally cure in just a minute or two, while the whole process takes about 4-6 minutes, depending on part size. After removal from the mold, components made from DCPD require no additional curing.
Finishing DCPD
Parts made via the DCPD RIM process create an easily paintable surface that is glossy and smooth. Paints readily adhere well to exteriors made from DCPD, allowing manufacturers to color them in just about any shade possible. The DCPD RIM process offers one of the most efficient means by which components that are lightweight, strong, and durable can be made quickly and with great efficiency.
To find out whether molded DCPD may work for your next project and to discuss how we can help, please contact Osborne Industries today.