A Comprehensive Guide to Heat Resistant Plastics
May 10, 2021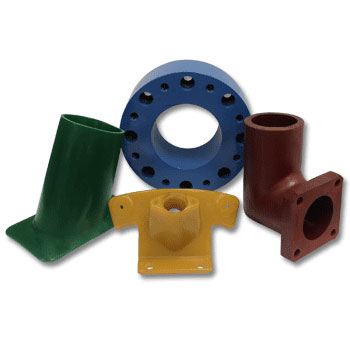
High Performance Composites Now Available in Custom Colors
September 14, 2021In general, plastics are classified as either thermoplastic or thermosetting plastics. Thermoplastic materials form easily with pressure and heat, which then become solid upon cooling. These materials can also be reprocessed into new forms when exposed to additional pressure and heat. Thermosetting materials, however, act more like concrete, and thus cannot be reshaped once processed and molded. Due to their versatility, the use of thermoplastics is far more common in society. However, thermosetting materials are often better suited for specific industries and applications.
Plastics are made up of molecules known as polymers, which are essentially just long chains of smaller molecules called monomers. These polymers are termed as either amorphous or crystalline, depending on their properties. Amorphous plastics typically have their polymers oriented randomly, tending to be tougher and more resistant to impact. When these polymer chains occur in an orderly and densely packed fashion, they are considered crystalline; these polymers typically offer better chemical resistance properties but tend to be less flexible.
These differences in plastics become far less clear, however, when considering formulations that contain both amorphous and crystalline material. The chemical industry requires that plastics be chemical-resistant, which would require crystalline polymers, though the rigors of industrial use mean the toughness endemic in amorphous polymers also offers advantages. For this reason, the chemical industry often uses distinctive types of plastics for different applications, including chemical-resistant polyolefins, fluoropolymers, rigid vinyl, polyphenylene sulfide (PPS), polyetheretherketone (PEEK), and polydicyclopentadiene, also known as pDCPD or DCPD.
Types of Plastics Used in the Chemical Industry
Certain types of plastics work better when exposed to harsh chemicals. These plastics have properties that make them chemically resistant, though what and how they are used depends upon certain other characteristics.
Chemical-Resistant Polyolefins
Polyolefins are thermoplastics, with polypropylene (PP) and high-density polyethylene (HDPE) the two types most commonly used for chemical applications.
These two polyolefins:
- Can easily be shaped with woodworking tools
- Join effectively using thermoplastic welding
- Resist chemicals well at room temperatures
Polyolefins tend to soften at higher temperatures and change form when subjected to repeated mechanical stressors. Because of their relatively low strength and stiffness, chemical tanks made from these plastics tend to be reinforced with metals.
Applications include:
- Cabinets in clean-rooms and laboratories
- Food processing equipment
- Tanks
Fluoropolymers
Classified mechanically as either thermosets or thermoplastics, these stable polymers offer enhanced resistance to chemicals while also handling hotter environments well. Also used in manufacturing semiconductors and in the pharmaceutical industry, the fluoropolymers used in the chemical industry include polytetrafluoroethylene (PTFE), polyvinylidene difluoride (PVDF) and ethylene chlorotrifluoroethylene (ECTFE).
These materials:
- Resist a wide variety of chemical compounds
- Are available in hard and soft gradients
- Feature friction-reducing properties
Applications include:
- Tanks, valves and piping for harsh chemicals
- Wet benches designed to resist acids and solvents
Rigid Vinyl
Thermoplastic types of rigid vinyl include polyvinyl chloride (PVC) and chlorinated polyvinyl chloride (CPVC), which offer better strength and stiffness than polyolefins while being less susceptible to heat. Rigid vinyl material also bonds well with solvent cement and allows joining via welding with hot gas, so it is often used in piping systems.
PVC offers:
- Economically-priced mechanical properties
- Grades of variable toughness
- A transparent grade of PVC offers comparatively enhanced chemical resistance properties when compared to other clear plastics.
Other applications include:
- Clean-room applications
- Machine guards
- Safety glazing
CPVC offers:
- Ability to operate at generally higher temperatures than PVC
- Better glass transition temperature than standard PVC
- Grades with superior impact-resistance
- Higher heat deflection temperatures than typical PVC
Applications include:
- Chemical tanks
- Fume hoods
- Laboratory workstations
Other High-Performance Plastics
High-performance plastics like polyphenylene sulfide (PPS) and polyetheretherketone (PEEK) offer greater strength, stiffness and dimensional stability. PPS is a semi-crystalline thermoplastic used in high temperature engineering, with a melting point of 536° F (280° C). PEEK provides resistance to both radiation and chemicals, while operating effectively in temperatures of up to 480° F (249° C) and in steam or hot water without compromising its physical integrity.
Both PPS and PEEK:
- Are often required for use with harsh chemicals in hot environments
- Can be formulated with additives to better resist friction and wear
- Maintain strength at higher temperatures
- Resist most industrial chemicals
While PEEK offers better mechanical properties and can operate at higher temperatures, PPS is less expensive.
Properties of pDCPD Plastic
Polydicyclopentadiene (pDCPD) plastics are a category of thermoset polymers that remain in a cured form. These DCPD plastics, along with other thermosets, resist melting because they are made with two dissimilar liquids, which fosters a high rate of crosslinking between the molecular chains and helps resist heat.
pDCPD plastics allow a great deal of freedom when it comes to design, as the limits on weight and size are wide-ranging. Components made from pDCPD plastics can range in thickness from 0.1 in. (2.5 mm) to up to a foot, while surface areas can range from a single square foot (approximately .093 square meters) to 140 square feet (approximately 13 square meters). Components with varying wall thicknesses and molds with ribbed surfaces are also possible with pDCPD plastics.
Parts with variable wall thickness and molded-in stiffening ribs are possible. Molded bosses and fasteners reduce secondary assembly operations. Good adhesion and machining quality extend the usefulness of pDCPD parts.
Other properties include:
- Extremely low viscosity allows easy processing
- Great thermal stability
- High breakdown strength
- Impressive mechanical strength and fracture toughness
- Low dielectric constant and loss
- Outstanding impact resistance
Unlike conventional thermoset plastics like silicone, polyester, polyurethane and epoxy, PDCPD plastics have a relatively low dielectric loss and constants, which are undesirable for high voltage and high-frequency applications.
Applications for pDCPD plastics include:
- Agricultural equipment components
- Chemical processing equipment that requires corrosion-resistance
- Conveyancing trays
- Equipment used in water treatment
- Fan shrouds and under-hood parts for transportation
- Housing for instruments or machines
- Large containers used for waste
- Panels for bodies of busses and large trucks
- Septic tanks
Contact the Professionals at Osborne
Osborne Industries offers more than 25 years of experience molding pDCPD, with a wide range of Reaction Injection Molding (RIM) equipment that will meet all your specific production requirements. Our expert team brings unique technical expertise in the chemistry of pDCPD, combined with the skills of dedicated craftsmen to help transform your vision into reality. To request a quote for your pDCPD molding project, please contact us today!