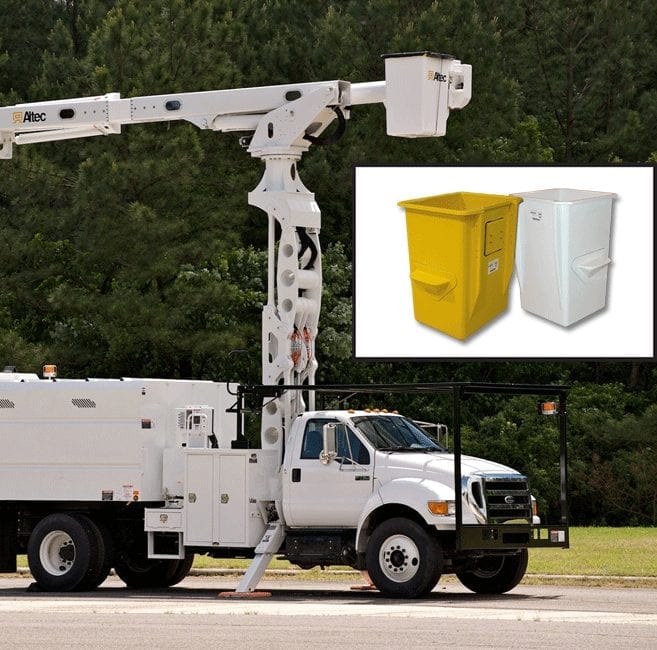
RTM and RIM Material Selection for Industry Applications
October 8, 2019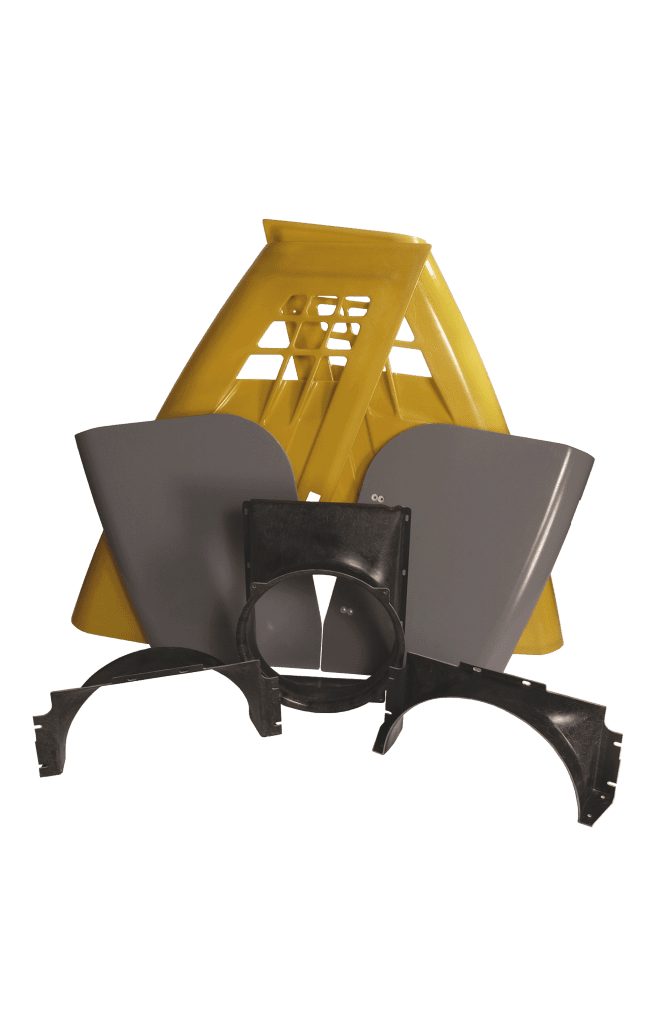
Thermosetting Plastic vs Thermoplastic Applications
January 8, 2020Plastic design guidelines are crucial for polydicyclopentadiene (pDCPD) molding because they allow for easier part moldability, reduce overall production time, and help to ensure the quality of a final product. We’ve outlined some fundamental guidelines you’ll want to consider when preparing pDCPD parts for reaction injection molding.
What is Reaction Injection Molding?
Reaction injection molding (RIM) is a thermoset plastic molding technique where two liquid reactants – an isocyanate component and a polyol resin mixture – are injected into a metal mold at relatively high temperatures and pressure. The mold is composed of two halves that are separated once the material reaction has taken place inside. Reaction time is typically just minutes long, making for more efficient part production.
What is Plastic Product Design?
Plastic part design involves creating a geometry that is not only functional but cost-effective to produce. To make this happen, the design process needs to be determined early on to avoid running into any conflicts with the primary product design elements: geometry, material, and manufacturing methods.
Plastic Design Guidelines for Reaction Injection Molding
Below are a few considerations to keep in mind when determining plastic part geometry for pDCPD.
Visible Surface Considerations
It’s important to understand that a higher quality surface is obtained on the hotter mold half – consider an outer visible surface (A) and inner/back surface (B). The higher quality surface requirements would be completed for side A, which is the cavity side or hotter side of the mold, with side B formed by the core of the tool which is the cooler side of the mold.
Thickness
The minimum thickness suggested for pDCPD is 3mm, based on the temperature peak during polymerization. The polymerization process releases heat that allows the material to reach its ultimate properties by fully converting. Any thickness less than 3mm results in dramatic heat loss in the mold, affecting its physical properties, and rapid change in part thickness may cause a shrinkage effect.
Polymerization Shrinkage
As noted above, polymerization releases heat that directly affects the physical properties of a mold. Shrinkage caused by polymerization depends on various factors, but is primarily determined by the amount of material and temperature profile of the tool being used. Shrinkage should be considered early in the design process to prevent uneven thickness distribution, distortion, and aesthetic issues caused by shrink marks.
Ribs
Ribs are used to stiffen a part without compromising its weight, though there are some drawbacks to this method, specifically demolding, difficulties in mold filling, and shrink marks. You can work to reduce shrink marks by adjusting the rib to skin thickness ratio, with the usual practice of hiding shrink marks under the part’s design features recommended whenever possible.
Bosses
Bosses provide fixation points for a molded part, so the same design rules for ribs apply to bosses as well. If you’re looking to avoid shrink marks, an alternative to molding a single-piece part with ribs or bosses is bonding a reinforcing element to one side of the surface.
Fillets and Radii
It’s recommended to include generous corner radii and fillets to prevent sharp corners, which can trap bubbles and create stress concentrations.
Edge Design for Deflashing
Deflashing any sharp edges of a part may result in roughness leftover. To prevent rough edges from deflashing, it’s best to maintain regular thickness of the molded part.
Draft
The purpose of a draft is to facilitate part demolding and help prevent any surface damage that could be caused by the mold. Generally, a minimum draft angle of 3° is suggested for the A-side and 1.5° on the B-side of the mold. If shrinkage occurs, there may be no draft on the A-side and you should consider increasing the draft angle to help facilitate demolding.
Undercuts
Undercuts commonly cause problems during the demolding stage, with the standard solution being a movable block (or blocks) within the mold.
Molded Openings
Molded openings are easily able to be incorporated into a pDCPD part, though appropriate venting of the part’s opening must be considered.
Mechanical Fastening
The most common way to assemble a pDCPD part is by using mechanical fasteners – this includes inserts or self-tapping screws, with the most popular type being overmolded or post-fixed inserts that provide reusable threaded connections. Any slots or holes used for assembly may need washers or spacers to help prevent creep. Other fasteners, like cage nuts or clips, don’t require any special design.
Contact the Professionals at Osborne Industries
Osborne Industries has the capability to manufacture pDCPD parts that are of top-notch quality. Our efficient production methods mean our RIM services can compete economically with other processes while allowing you to inexpensively market test concepts and increase production.
Please contact us online to learn more about plastic design guidelines for pDCPD and our reaction injection molding services. If you have a project in mind, you can request a quote today!