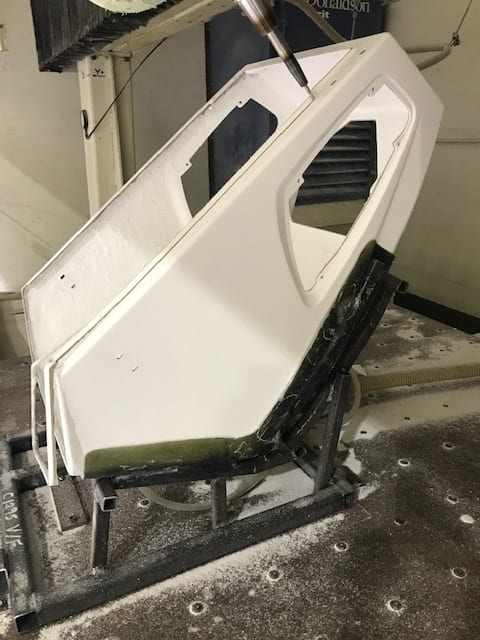
A Guide to CNC Machining Services
February 1, 202115 Advantages of Choosing Lightweight Plastic Composites
March 15, 2021Plastics encompass a wide array of materials and molding processes used to create finished parts. Typical injection molding involves heating thermoplastic or thermosetting plastic polymers and injecting them into a mold where it conforms to the mold cavity, cools and hardens. Other molding processes, like Resin Transfer Molding (RTM), involve injecting or spraying liquid thermosetting materials into a mold with reinforcing fibers, like fiberglass. Typical plastic molding can be done two ways: either by closed molding or open molding. In simple terms, plastic resin exposed to the atmosphere during curing is known as open molding, while that which is not exposed to air during curing is known as closed molding. Each type of molding has its place within the plastics industry, with advantages and disadvantages for each.
Open Molding Process
The open molding process is generally less expensive since it doesn’t require the resin to be sealed off from the surrounding environment. The three main types of open molding processes are:
- Hand lay-up molding is the least expensive and most common open molding method, with fiber reinforcement placed into a single mold cavity and resin applied via hand with rollers or brushes. It’s used for a variety of large and small products, including storage tanks, showers, tubs and boats.
- Spray-up molding is similar to the hand lay-up method, though it uses a chopper gun and other special equipment to cut reinforcing material into shorter fibers before adding it to the resin mixture on the mold’s surface. As it involves automation, this method tends to be used for producing on large scales.
- Filament winding molding involves applying fiber strands that are saturated with resin to reinforce it in a cylindrical mold that rotates. It’s less labor intensive than other types of open molding methods and is used in the manufacture of such things as piping, stacks, chemical storage tanks and rocket motor casings.
Because tooling costs for open molds tend to be lower, open molding is more widely used for short production runs. It’s typically used for larger products for which automated processes are unsuited or products made in such low volumes that the cost of automating the process isn’t justifiable. As only one side of a finished part created in an open mold is smooth, the process is not appropriate for parts that require a smooth finish across all surfaces.
Closed Molding Process
For most larger scale plastic production, closed molding processes are more advantageous. With closed molding methods, dry reinforcing material can be put into the mold, which is then closed. The plastic resin is then put into this enclosed cavity, using either a vacuum or pressure pump to infuse it with resin. Once the material cures, the mold is opened and the plastic part or product is removed. Closed molding via processes like Reaction Injection Molding (RIM) often do not utilize a reinforcing material, as the materials used are often structurally sound without reinforcements. The following are types of closed molding processes:
- Centrifugal casting or rotational molding uses a rotating mold, where reinforcing material and/or resin solidify against the inside surface of the mold. The centrifuge holds the material in place as it hardens and cures, and is used to produce hollow objects, such as piping.
- Compression molding involves sandwiching composite materials between two matching molds, using heat and intense pressure until the part cures. Allowing for quick molding cycles and highly uniform parts, it’s used in the manufacturing of complex polymer components reinforced with fiberglass.
- Continuous lamination combines resin and fibers in a highly automated process, sandwiching the two between two carrier films that are then steered along a conveyor. After forming rollers form these into sheets, the resin is cured and used to make paneling and sheeting.
- Pultrusion allows for the formation of long, consistently shaped objects, using continuous strands that are moved through and soaked in resin baths. These elongated shapes are then pulled through heated steel molds and molded into lengths. The process can be easily automated, and is used to manufacture solid or hollow bars, tubing, channels, pipes or rods.
- Reaction injection molding heats and combines multiple liquid resins separately as they are injected into a closed mold. Composites made through this process feature lower manhours, quicker cycling, lower scrap rates and low-pressure mold clamping. An almost identical process called “reinforced reaction injection molding” introduces reinforcing material into the composite mixture. This process allows fashioning of products that include body panels, vehicle bumpers and fenders, spoilers, roofing fascia and floor paneling.
- Resin transfer molding, also referred to as RTM, involves loading reinforcement material, often fiberglass, into closed molds, which are then clamped before pumping resin under pressure into the cavity through injection ports. This procedure allows manufacturers to produce complex parts with smooth finishes, and can be applied to either simple or highly automated processing. This process allows for limitless combinations and orientations to be used, including three dimensional reinforcements. It’s used to make yacht hulls and decks, windmill rotor blades and for various purposes in the automotive, aerospace, military, and construction industries.
- Vacuum bag molding improves the laminate’s mechanical properties, by which liquid resin is applied to reinforcing fibers before a vacuum is used to force out excess resin and trapped air to compact the laminate. This process offers greater adhesion between sandwiched layers and helps eliminate excess resin buildup often found with the open molding hand lay-up technique. It’s typically used in manufacturing products across a wide array of industries, though its molds are similar to those used with standard open mold methods.
- Vacuum infusion processing uses vacuum pressure to infuse resin directly into laminate, using inexpensive and minimal equipment. Used for low-volume products, this technique typically is used when manufacturing very large structures, producing lightweight laminates while reducing emissions. It’s a more recently developed technique that is used to manufacture large objects such as wind turbine blades, boat hulls or structures in the aerospace industry.
When compared to open molding, closed molding techniques allow manufacturers to make better parts with less waste. Along with ensuring parts come out more consistently, they also look better cosmetically, requiring less work after the molding process.
Closed molding processes tend to be more expensive, however, as they require a greater capital investment. To counter the larger expenditure, closed molding systems produce significantly less emissions, so they assist manufacturers in meeting emission requirements while reducing the need for protective equipment and lowering labor costs due to increased automation.
RTM & RIM Molding Processes
Two types of closed molding processes in which Osborne specializes are resin transfer molding (RTM) and reaction injection molding (RIM). Using proprietary and custom techniques, Osborne provides manufacturers with economical composite molding, capable of producing extended runs through unique in-house molding processes.
Having the ability to produce composite RTM tooling in house, Osborne offers much greater cost-effectiveness when compared to compression equipment. The company’s RTM molds provide customers a better return on investment than simpler open molds, and Osborne can easily match production capacity even on larger-scale projects.
Durable and inexpensive, Osborne’s RIM molds allow greater flexibility in earlier stages of production while allowing conversion to high-speed metal tooling for high-volume production. Osborne’s RIM molding process allows manufacturers to test new designs, tie investment to market demand and increase production as demand increases.
Contact the Closed Molding Experts at Osborne
Osborne offers composite molding that can make quality components quickly and efficiently, especially when compared to some other tooling and processes used by competitors. For more information about our plastic molding capabilities for your next project, contact the experts at Osborne Industries today