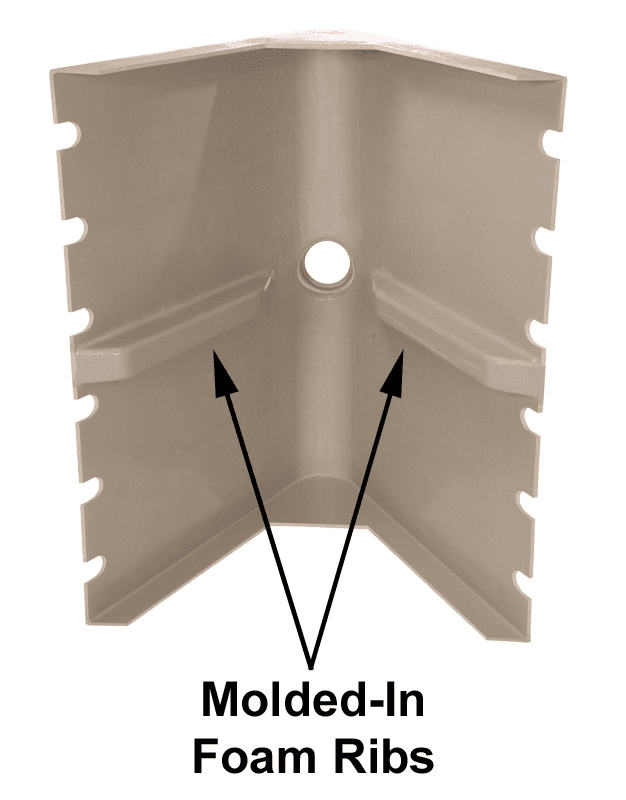
Combination of Composite Materials in Design
July 20, 2020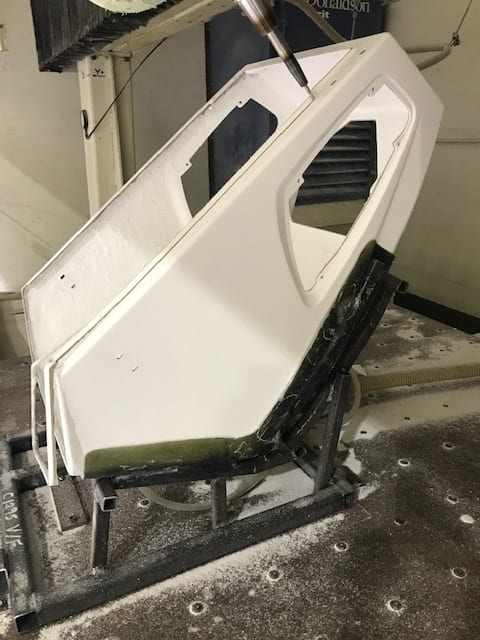
A Guide to CNC Machining Services
February 1, 2021It’s no secret that both thermosetting plastics and thermoplastics play a significant role in the world today, but with so many different material properties, it can be difficult to determine which one is appropriate for a specific application. How do you determine which material is best?
Two popular plastics with somewhat similar material properties are UHMWPE and pDCPD, both of which offer unique benefits to fabrication and the applications in which they are used. Below, we compare and contrast these two key players to help you decipher which will work best for your application.
UHMWPE vs pDCPD: What’s the Difference?
Ultra High Molecular Weight Polyethylene, commonly abbreviated as UHMWPE, is a thermoplastic subset of polyethylene. This material is versatile, known for its toughness, with a strength-to-weight ratio anywhere from 8-15 times greater than steel, and 10 times the resistance to abrasion. UHMWPE is self-lubricating, has very low moisture absorption, and is renowned for its machineability.
Polydicyclopentadiene, referred to as pDCPD, is a liquid thermoset resin. It has excellent elasticity, is lightweight, and extremely resistant to abrasion, corrosion and impact. pDCPD is excellent for large, shaped parts due to its freedom of design. It’s also easily paintable and its surface works well for adhesion.
Advantages of UHMWPE
There are many benefits that come from utilizing UHMWPE. Some of these advantages can include:
- Abrasion resistance
- Chemical resistance
- Dielectric properties
- FDA-approved (for medical and food industry use)
- High stress resistance
- High resistance to cracking
- Low specific gravity (floats in water)
- Non-staining
- Self-lubricating
There are few disadvantages to consider, though, as no material is perfect. UHMPE does have a lower melting point compared with many polymers, so it’s not ideal for high-temperature applications. It can develop “creep” (or deformation) over time when exposed to a constant load, and material cost can also sometimes be a deterring factor.
Advantages of pDCPD
The polymerized material of pDCPD allows for a wide range of performance characteristics and mechanical properties. Some of these beneficial characteristics include:
- Abrasion resistance
- Chemical resistance (especially to alkalis, acids, degreasers, and electrolytics, and other caustic solutions)
- Corrosion resistance
- Flame retardance
- Flexibility
- Heat resistance
- High tensile strength
- High impact strength
- Moldability and versatility in using molded-in components
When compared with UHMWPE, the creep factor of DCPD is often significantly less when exposed to repetitive mechanical stress. Although actual creep is dependent on application and factors like part geometry, temperature, and time, DCPD’s properties related to creep, like heat deflection temperature (HDT) and glass transition temperature, are undoubtedly superior.
UHMWPE | pDCPD | |
Heat Deflection Temperature (HDT) | 82° C (180° F) | 120° C (248° F) |
Glass Transition Temperature | 136° C (277° F) *Melting Point* | 155° C (311° F) |
Common UHMWPE Applications
Ultra High Molecular Weight Polyethylene boasts a diverse range of applications; because there are so many benefits, the material can be used for a variety of parts. This is especially true for applications where friction tends to be high because of its self-lubricating properties.
Some common applications and industries in which this material is used can include:
- Automotive industry
- Chemical industry
- Civil engineering
- Earthmoving equipment
- Food processing equipment
- Manufacturing equipment
- Medical applications
- Sports equipment (such as boating, fishing or skiing)
Common pDCPD Applications
pDCPD’s ease of moldability and flexibility in design allow it to be widely used for commercial and industrial applications. Large structural parts that replace inferior thermoplastics or heavy, corrosion-prone metals are perfect for pDCPD. Some applications include (but are not limited to):
- Agricultural equipment
- Body panels for transportation vehicles
- Construction equipment
- Off-highway equipment and machinery
- Components for chlorine and other caustic solution generation
- Portable industrial equipment
- Utility and in-plant service vehicle parts (like forklifts)
- Medical equipment
Contact Osborne
For over 45 years, Osborne has developed its experience in molding a variety of materials, most notably thermosetting materials like pDCPD. Our capabilities range across a variety of industries, each of which requires unique part specifications and material production. Buyers and engineers look to Osborne for material expertise and our experience in successfully converting metal or thermoplastic parts to high-performance thermosetting polymers.
No matter how large or small, Osborne can customize your design or idea and create finished products to your exact requirements. Let us help you get your project started by contacting us today!