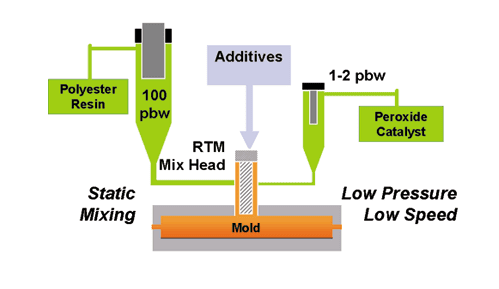
How the Resin Transfer Molding Process Works
March 16, 2017Osborne Installs Automated Fiberglass Cutting System
May 24, 2017Primary Difference Between Thermoplastic and Thermoset
Though “thermoplastic” and “thermosetting plastic” sound very much alike, the difference between thermoplastics and thermoset plastics is significant. Each has very distinctive applications and properties, along with differences in how they are processed or manufactured. Understanding the difference between thermoplastics and thermosetting plastics can help both manufacturers and product designers improve upon their products.
Basic Difference Between Thermoplastic and Thermosetting Plastic
Thermoplastics and thermosetting plastics are both polymers but behave differently when exposed to heat. The key difference between thermoplastic and thermosetting plastics involves the fact that thermoplastics can melt under heat after curing, while thermoset plastics keep their form and remain solid under heat once cured. The low melting point of materials made from thermoplastics makes it ideal for applications that use recycled material, while products made from thermoset plastics can withstand high temperatures without losing their shape, so are inherently considered more durable.
Thermoplastics Curing Process
When heated, thermoplastics soften and eventually become fluid. Processing thermoplastics involves no chemical bonding, which allows the material to be remolded and recycled without affecting its material properties. The properties of thermoplastic resins can vary significantly, but materials made from them tend to resist shrinking, along with offering considerable elasticity and strength. Typically, thermoplastic resins are used for a wide range of applications, from industrial components in machinery to the plastic bags used in retail stores.
Advantages of thermoplastics include:
- Adheres well to metal
- Allows for quality aesthetic finishes
- Capable of reshaping after curing without much effect to material properties (recyclable)
- Chemical and detergent resistant
- Good electrical insulation properties
- Enhanced anti-slip properties
- Resistant to impact
- Offers options for both hardened crystalline and rubbery surfaces
- Resistant to chipping
- Resists corrosion well
Disadvantages of thermoplastics include:
- Ability to soften when heated makes it less suitable for some applications
- Often more expensive option than thermosetting polymers
- Commonly used thermoplastic polymers include polyvinylchloride (vinyl or PVC), polypropylene (PP), polystyrene (PS), polyethylene (PE), polycarbonate (PC) and polyethylene theraphthalate (PET).
Thermoset Curing Process
Usually produced using the Reaction Injection Molding (RIM) or Resin Transfer Molding (RTM) processes, thermoset plastic polymers combine together to form permanent chemical bonds during the curing process. This chemical reaction forms bonds between monomer chains within the material, keeping it from returning to its original liquid state when reheated. This difference between thermoplastic and thermoset plastics makes the latter better for applications where heat is a factor, such as in housings for electronics or appliances and chemical-processing equipment, as it has greater structural integrity due to its resistance to both heat and chemicals. Thermoset plastics also possess several improved mechanical properties, with products made from it better at resisting deformation and impact.
Advantages of thermosetting polymers include:
- Allows for flexible product design
- Can be molded with different tolerances
- Capable of varying wall thickness to improve structural integrity
- Components usually cost less than those fabricated from metals – especially for large equipment body panels
- Excellent electrical insulation properties
- Greater resistance to high temperatures
- High dimensional stability
- Highly resistant to corrosion
- Low thermal conductivity
- Lower costs for setup and tooling compared to thermoplastics
- Offers high strength-to-weight ratio to improve product performance
- Water-resistant
- Wide choice for coloring and surface finishes
Thermosetting polymers disadvantages include:
- Can neither be reshaped nor remolded
- Not recyclable
Commonly used thermoset plastics include polyepoxides (epoxy resins), phenol-formaldehyde (PF or phenolics), polysiloxane (silicones), and polyethylene terephthalate (polyesters), polyurethanes, polydicyclopentadiene (pDCPD), and structural foams.
Aesthetic Difference Between Thermoplastic and Thermosetting
Though some may argue thermoplastics offer better aesthetics than thermosets, thermosetting polymers still offer better aesthetics than other alternatives like metals. Both RIM and RTM techniques readily accept secondary painting, but also allow in-mold painting or coating. This involves spraying coatings or gel coat directly into a mold before the thermosetting polymers are injected into it. This process bonds the paint or coating to the surface, offering better adhesion to prevent chipping, cracking or flaking even when exposed to harsh weather conditions. This makes in-mold coatings of thermosetting materials ideal for such applications as construction machinery or other material that needs to withstand extreme conditions.
Industries Using Thermoplastic and Thermosetting Polymers
With the basic differences between thermoplastic and thermosetting plastics established, let’s look at what applications each type of polymer has within various industries.
Applications for Thermoplastic Polymers
Thermoplastics can be found in virtually any industry with products ranging from milk jugs to piping systems. As thermoplastics are capable of withstanding corrosive conditions, they work well as a substitute for metals, but cannot withstand high temperatures as well as thermosets.
Applications include:
- Fabricating ropes or belts
- Insulating electrical cabling
- Liquid storage tanks
- Protective covers for rigid equipment
- Other industries utilizing thermoplastics include construction, electronics, medical and biomedical, food and beverage, chemical, automotive, plumbing, and many more.
Applications for Thermosetting Polymers
Offering an excellent combination of chemical resistance, structural robustness and thermal stability, thermosetting polymers are widely used throughout a range of industries, as they offer an economical means to meet many production specifications. They are easily formed into complex geometric shapes that fabrication of metal components cannot easily achieve, and components made via RIM and RTM techniques allow for considerable consistency in the fabrication process.
Applications include:
- Chlorine and other chemical generation piping, fittings, or cell covers
- Electrical or medical equipment housings and components
- Heavy construction or transportation equipment like doors, panels, or housings
- Livestock feeding troughs and other agricultural products
- Motor vehicle and tractor parts
- Military vehicle components
Sectors that use thermosetting polymers include the adhesive and sealant, aerospace and defense, appliance and electrical, automotive, energy, and construction industries.
Contact Us
Understanding the difference between thermoplastic and thermoset plastics is essential for both manufacturers and product designers alike. To learn more about Osborne’s capabilities with thermosets and how they can offer added benefits to your products or parts currently being made of metal or thermosetting materials, please contact us today.
Learn More About These Plastic Molding Processes