15 Advantages of Choosing Lightweight Plastic Composites
March 15, 2021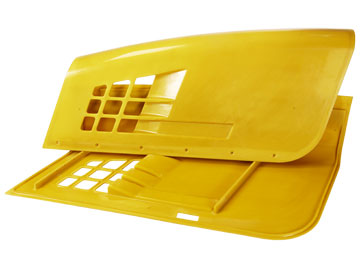
Plastics Used in the Chemical Manufacturing Industry
July 11, 2021Heat resistant materials are important for components that need to withstand high temperatures, whether the heat is generated artificially – as is the case with materials exposed to continuous friction or abrasion – or naturally due to climatic or environmental extremes. While both metals and ceramics have heat resistant qualities, metals corrode easily and ceramics are extraordinarily brittle. Heat resistant plastics have unique properties that allow them to outperform metals and ceramics. Along with resistance to high temperatures, heat resistant polymers will neither corrode like metals nor break like ceramics, and tend to be more durable than other materials.
Advantages of Heat Resistant Plastics
Heat resistant plastics, like those belonging to the family of thermosetting plastics, tend to perform well in both extreme temperatures and when exposed to chemicals. In contrast, thermoplastics melt easily at high temperatures. Though easily recycled, thermoplastics cannot be used for components that experience high temperatures.
Many heat resistant polymers are made using the reaction injection molding (RIM) and resin transfer molding (RTM). Both RTM and RIM plastics can be reinforced with fibers such as aramid, carbon, glass or graphite. These fibers allow them to withstand deformation due to high temperatures, abrasion, weather, and even natural deterioration.
Heat resistant and semi-heat resistant plastics, including both thermo and thermosetting materials, include:
- Amorphous plastics include most clear plastics, including polycarbonate, polysulfone, PETG, ABS and acrylic. They are easy to mold and bond well with adhesives. These plastics also hold their shape better when exposed to heat and resist impact, though they are more prone to stress fractures and tend to break more easily than semi-crystalline polymers.
- Semi-crystalline plastics are typically used for plastic components, and include polypropylene, fluoropolymers, nylon, acetal and polyethylenes (LDPE, HDPE, UHMW-PE). These heat resistant polymers work great for structural and bearing applications, and tend also to resist friction and chemicals. However, semi-crystalline polymers don’t bond or mold easily, and have only average resistance to impact and a very narrow temperature melting point.
- Themosetting plastics, like those molded at Osborne, are often used across a variety of industries for things like large machine body parts and covers, vehicle fenders and bumpers, and others subject to extreme conditions in the field. These materials include polyester, vinyl ester, DCPD (dicyclopentadiene), polyurethane, and more.
Often, heat resistant plastics are used in place of metals for components because they are lighter weight and more resistant to chemicals, abrasion, and impact.
Contact Osborne Industries
Are you needing a heat resistant plastic component for your equipment or project? Osborne offers more than 45 years of custom molding experience, specializing in heat resistant DCPD, RIM and RTM molding. Our expert team will create a design and final product that fits your specifications. To learn more about our project capabilities, please contact us today!