Reaction Injection Molding 101: What is Dicyclopentadiene?
December 15, 2021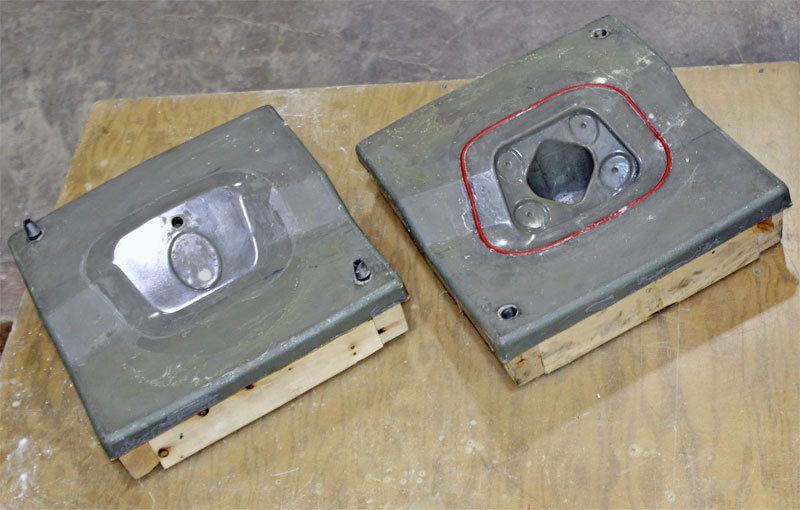
Ask the Thermosetting Experts: Do I Need a Prototype?
March 15, 2022The plastics industry has a long history in the USA, going back to the early part of the 19th century. In 1907, plastics made from synthetic materials were first developed by Leo Baekeland in the USA. Injection molding machines were invented even earlier, in 1872, by a prolific inventor by the name of John Wesley Hyatt, a New Yorker.
Today, the top producer of plastics is China. While the Chinese produced approximately 31 percent of plastic products in 2019, NAFTA (North American Free Trade Agreement) members – Canada, Mexico and the USA – accounted for 19 percent. This isn’t surprising, as China has largely become the world’s factory, producing an outsized portion of goods globally. Yet the American plastic industry is one of the strongest, and USA injection molding continues to lead the world in technological advancements.
Made in the USA: Injection Molding Advantages for Product Manufacturers
The world is connected globally and barring a catastrophe that returns humanity to the stone age, this is unlikely to change in the near future. As such, manufacturers can source products and services from anywhere in the world, including plastics produced by various methods like injection molding, resin transfer molding (RTM), and reaction injection molding (RIM). Benefits the USA offers over competing countries are myriad, with the following seven reasons being just the tip of the iceberg.
Advantages of working with USA injection molding companies include:
1. Control & Ownership of Molds
In the USA, plastic molds and molding forms for the most part don’t belong to the company tasked with producing them. Though a handful of American toolmakers deal with prototypes, and low output production runs retain ownership of the molds they produce, ownership almost exclusively belongs to the end-product manufacturer. As long as they remain in good standing, product manufacturers shouldn’t have any problem moving their molding processes to another facility, regardless of whether they’re American or foreign plastic manufacturers.
2. Quality & Consistency
Excellent mold makers exist worldwide, though there’s a reason that the plastics industry has, unlike many other industries, continued to grow in the USA. Plastic molding by American companies is generally more consistent and of better quality, especially with processes like injection molding and reaction injection molding (RIM). The American-based Society of Plastics Industry (SPI) has set high molding standards for the industry to ensure superior workmanship, a crucial element in many products made from plastic. Products made with American molds also often undergo more stringent inspection and must meet higher standards than those made abroad.
3. Shrinking Price Differential
Many product manufacturers who chose offshore production did so because of lower costs, particularly regarding labor. Yet in places like China, where much plastic production moved during the 20th century, rising wages offset these benefits. Furthermore, an increasing number of companies are finding that the costs of things like raw materials, shipping, complex regulations, and even corruption, add to their costs. This is starting to prompt a move back to the USA, where composite molding is becoming increasingly economical.
4. Supply Chain Issues
The Coronavirus pandemic made a mess of the supply chain worldwide, including for the plastics industry. Injection molding customers that depended upon Chinese companies and other foreign sources for plastic components found themselves unable to continue production due to logistical difficulties. Add to these container shortages, factory fires, and a container ship blocking the Suez Canal, and logistics quickly turned into a nightmare. Examples like this that cause disruptions in production point towards the need for manufacturers to source injection and other plastic molding companies closer to their production facilities.
5. Strategic Advantages
The oil and gas sector largely fuels the American plastics industry, as several common plastics require the use of ethylene, which is made from natural gas. As natural gas is a plentiful resource in the USA, injection molding in the country benefits from easy access to petrochemical feedstocks. Plentiful American shale oil and gas reserves give the country an advantage in plastic production, which will be increasingly important for oil companies as transportation-related demand for petroleum decreases.
6. Innovation
American innovation hasn’t faded in the plastics industry, even after more than a century. Processing methods for plastics and materials that were developed in the USA, like injection molding itself, have continued to be used by manufacturers globally. Advancements in automation and 3D printing have shown how American ingenuity continues to drive technological advancement, along with the development of new types of plastics. In 2020, chemists from the Massachusetts Institute of Technology (MIT) produced a new, degradable polydicyclopentadiene (pDCPD) thermoset plastic, possessing a superior combination of corrosion and chemical resistance, durability, strength, and resistance to heat as compared to typical materials used in some injection molding.
7. Import Taxes & Trade Wars
Domestic production doesn’t incur import duties. In 2018, such duties were imposed on Canada, the European Union and Mexico regarding steel and aluminum imports. This affected the American plastics industry, which depends on such imports to support its manufacturing. That same year saw a trade war develop that affected many industries in both China and the USA. In total, approximately $200 billion in Chinese plastic products saw new import taxes, including molds, plastic machinery and components, pipes, hoses, flexible tubing, furniture, building products, luggage, and more.
USA Injection Molding by Osborne Industries
Osborne Industries specializes in thermoset plastics, particularly liquid molding using reaction injection molding (RIM) and resin transfer molding (RTM) methods. Our company has over 45 years of practical experience in composite production, which makes us the ideal partner for manufacturers who need to resolve challenging issues regarding plastics. Our experienced team at Osborne works with a range of materials and can formulate custom materials to meet the most demanding of applications. To learn more about our capabilities, please contact us today.